PROBLEMS WITH SIPS
WHAT IS A SIP?
A SIP is a composite panel, consisting of a thick insulating layer of rigid core foam, sandwiched between two layers of OSB woodfibre board, which is used as a building material for walls, floors and roof structures. Some of the arguments for building with SIPS include:
- Faster construction
- Cheaper pricing
- Factory Quality
- Improved U-Values
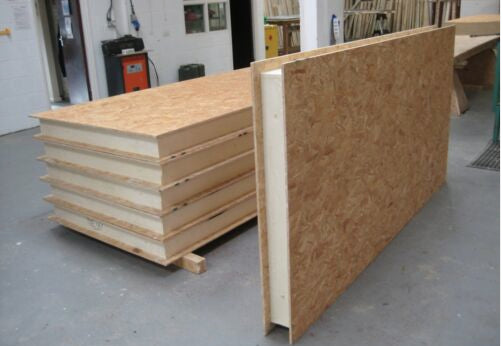
Should you use SIPS on your new Garden Room Office?
When we first started manufacturing garden buildings we looked at SIPs in great detail. Being open to any new technology and innovation, we compared the pros and cons of SIPs compared to Traditional methods of construction, after all some of the large U.K. House Builders use them, so the thought was that they must be good.
Here is what the process taught us about SIPS:
SIPs SAVE TIME
:
SIPs SAVE TIME :
The biggest advantage in using SIPs is mainly an installers advantage due to the time saved on-site. Think about it - if the company can install in 3 days instead of say 7, that’s a massive increase in productivity and thereby, profit. The team using SIPs has started a second installation before the company using Traditional methods has finished their first..! Conclusion: Big advantages to installers, but little advantage to the customer, other than the installers have come and gone a few days earlier.
SIPs PRICE ADVANTAGE
:
SIPs PRICE ADVANTAGE :
There are a number of SIPS panel suppliers around the UK, however most of these are large suppliers feeding the big builders. They are certainly cheaper to produce than a Traditional method so manufacturers of garden rooms and offices love them as they are able to offer competitive pricing or make bigger profit margins. Conclusion: Big profit advantage to the installer or possibly cheaper prices for the customer.
SIPs & SITE ACCESS:
SIPs & SITE ACCESS:
SIPs panels are large, typically at least 8’ x 4’ so access to site needs to be sufficient to get these components to the build location. Getting into tight spaces is sometimes impossible with these large panels. Conclusion: Some customers may not have sufficient site access for a SIPs built structure.
SIPs INSTALLATION
:
SIPs INSTALLATION :
Another advantage in using SIPs is that you do not need a highly skilled workforce to erect them. Very often a company will use low-skilled foreign sub-contractors for the installation. This saves the installer more money as this type of labour is much cheaper than time-served UK carpenters. Conclusion: Again the installers big advantage is in being able to use cheaper, unskilled workers to erect them rather than time-served tradesmen, making a bigger profit in the process.
SIPs & DESIGN FLEXIBILITY
:
SIPs & DESIGN FLEXIBILITY :
SIPs can work well when a building is designed to standard panel sizes so that orders placed with the manufacturing factory can be mass produced. This maximises factory efficiency but limits the overall design flexibility. Big factories don’t like small quantities of bespoke sizes. Prices and lead times increase. Conclusion: Standardised sizes will be pushed during the sale process and the customer persuaded that bespoke sizes will be much more expensive.
SIPs & THE WEATHER:
SIPs & THE WEATHER:
SIPs panels should not be allowed to get wet during construction because if water gets into the panels the moisture has no way to escape from the composite structure. This can build-in the problem of mould. Mould in any timber structure is a massive problem, but in a SIPS building it is unfix-able. Mould is also a serious health issue, and can significantly impact the well being of occupants. By contrast, in a Traditional timber framed wall, the structure is allowed to breathe, so the timbers can dry out even if moisture does get in during installation. Conclusion: SIPs built structures should not be erected during inclement weather, or they should be weather protected, due to the high risk of rainwater saturation becoming ‘locked-in’, resulting in mould propagation and subsequent structural rot.
SIPs & BREATHABILITY
:
SIPs & BREATHABILITY :
This is the biggest issue with building a garden room or office using SIP panels - it's so airtight that it becomes a sealed coffin. Yes, its got slightly better U-values (not that you'd notice the difference). But it can’t breathe, and neither can you. Yes, the large Housebuilders have in recent years started using SIPs, but they are subject to Building Regulations and must make their structures breathable using complex mechanical air flow & air replenishment systems. This is unrealistic in a garden room, these devices are too big, too complex and too costly to install. So moist air will just linger, and migrate into your plasterboard, creating long term mould issues. Some companies say they solve this problem by fitting an extractor fan in the wall and by providing an opening window. The only way this works is by leaving the window open, even in freezing winter..! Conclusion: Unless effective mechanical ventilation systems are installed (almost impossible in a garden room), in our opinion SIPs panels are not suitable for building garden rooms
FINAL CONCLUSION
So to summarise; companies supplying garden rooms will try to convince you that SIPs are a great idea due to their superior technical advantages. The truth is that the main advantages belong to the installer - quicker build times and low skilled labour, resulting in higher profits. Yes, they are marginally warmer than a Traditional timber structure, but in truth, not enough for you to notice.
But they will not mention the crucial disadvantage, the fact that they do not ‘breathe’. It’s a sealed box and, unless its ventilated, it could get very uncomfortable to work in as well as suffering the long-term problems mentioned with moist air and mould growth.
For the above reasons Rubicon rejected SIP based manufacturing early on in favour of the Traditional timber frame construction methods. These methods can take a little longer and require a more skilled workforce. But they have been proven over many decades, and crucially the resultant structures allow the timber frames to breathe (when built with correct membranes and venting techniques), whilst SIPs structures don’t. Our garden rooms and offices are designed and engineered to avoid the build up of mould and moisture over time, and we can still achieve similar levels of insulated U-Values and excellent air tightness far more reliably than you can with SIPS.
Think about it- given the above mentioned installer advantages, if we don’t think SIPs panels are suitable for building garden rooms or offices, why would you?
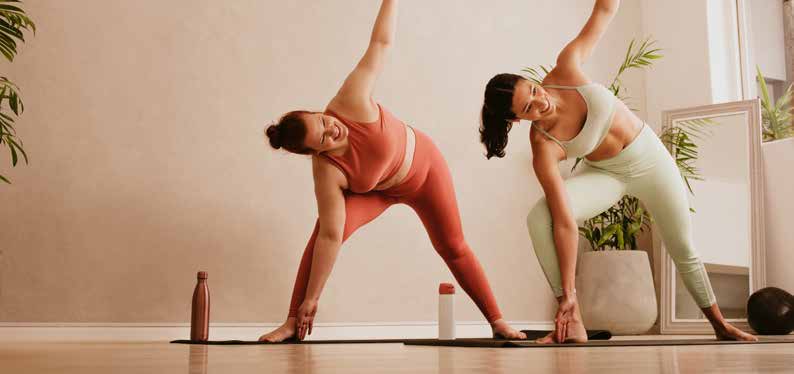
Where we operate
We primarily operate across the Chester, Cheshire, Mold, Buckley, Wrexham, Rossett, Wirral, Deeside, Flintshire, Denbighshire, North Wales, Llandudno, Colwyn Bay, Conway, Manchester, Stockport, Altrincham, Macclesfield, Lancashire, Liverpool, St Helens, Warrington, Birkenhead, West Kirby, Ellesmere Port, North West, Prestbury, Crewe, Nantwich, Preston, Malpas, Frodsham, Helsby, Heswall, Shrewsbury, Whitchurch, and Shropshire areas, but welcome enquiries from other areas within 70 miles of our Deeside base.
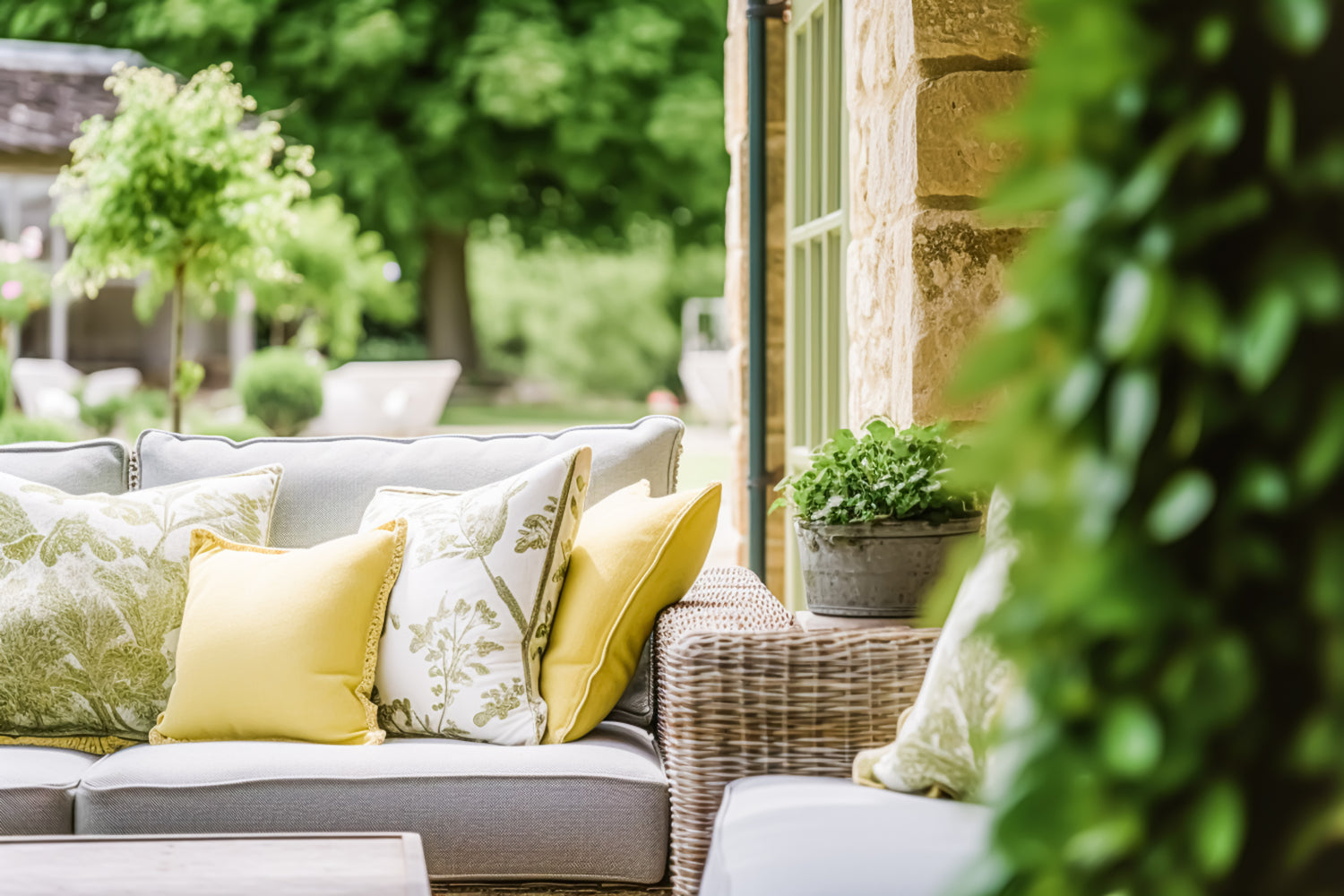
“From the moment we planned the garden room (gym) until the keys were handed over, the whole process was smooth, professional and problem free.”
Karen T